Both cast iron and cast steel are Fe-C alloys. Due to the different contents of carbon, silicon, manganese, phosphorus, sulfur and other chemical elements, they provide different metallographic structures and show many different mechanical properties and coinability. It is generally considered that the carbon content above 2% is cast iron, while containing 0.1-0.5% carbon is cast steel. Let us have a look at the differences between steel castings and iron castings according to their classification and application.
Cast iron
Gray cast iron. High carbon content (2.7% ~ 4.0%). Gray cast iron is the most widely used flake graphite cast iron (accounting for more than 80% of the total pig iron production). Carbon mainly exists in the form of flake graphite, which is gray in color, has a low melting point (1145 ~ 1250°C), and has a small shrinkage rate when solidified. Its compressive strength and hardness are similar to those of carbon steel, and it has good shock absorption. It is used to manufacture machine tool beds and cylinders Body, box and other structural Ural parts.
Vermicular cast iron. Gray cast iron obtained by creep treatment. Its precipitated graphite is worm-like, between scale stone and spherical. Its chemical structure is similar to that of gray cast iron, its mechanical properties are similar to those of cast iron, and its casting performance is between gray cast iron and nodular cast iron.
Can be used to make auto parts.
Tough iron. The nodular graphite gray cast iron obtained through spheroidization and inoculation is called ductile rock cast iron, which is a high-strength cast iron with near-steel comprehensive properties and is widely used in industrial fields. It has higher strength, better toughness and plasticity than ordinary gray cast iron.
Used in the manufacture of internal combustion engines, auto parts and agricultural machinery.
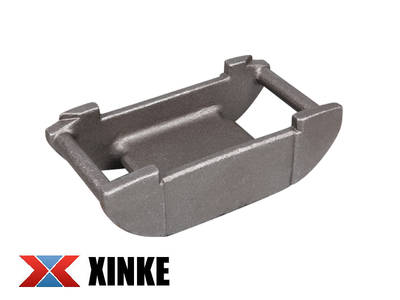
Cast steel
Cast steel is an iron-carbon alloy with a carbon content below 2.11%. Cast steel has good overall properties, weldability and workability, but it has poor shake and castability compared to cast iron. Cast steel can be divided into cast carbon steel, cast low alloy steel and cast special steel, according to the composition of chemical elements.
cast carbon steel. Cast steel uses carbon as the main alloying element and small amounts of other elements. It can be divided into cast low carbon steel (containing less than 0.2% carbon), cast medium carbon steel (containing 0.2%~0.5% carbon), and cast high carbon steel (containing more than 0.5% carbon). As the carbon content increases, its strength and hardness increase. Cast carbon steel has higher strength, plasticity and toughness, low cost, used in heavy machinery, used to produce a large number of parts, such as rolling machine frame, hydraulic machine base; to produce heavy bearing parts, such as pillows, side frames, wheels and railway vehicles of couplings.
Cast low alloy steel. Cast steel containing manganese, chromium, copper and other alloying elements (total content less than 5%). It has greater impact toughness, and better mechanical properties can be obtained through heat treatment. Cast low alloy steel has better performance than carbon steel, which can reduce the quality of parts and improve service life.
Cast special steel. Alloy cast steel is refined for special needs. It usually contains high amounts of one or more alloying elements to obtain specific properties. For example, high manganese steel containing 11% to 14% of manganese and manganese can withstand impact wear, mainly used in mining machinery, construction machinery wear parts; various stainless steels with chromium or chromium-nickel as the main alloy element, used for corrosion or in high Parts working at a high temperature of 650°C, such as valve bodies, pumps, containers or steam turbine casings for large-capacity power stations in the chemical industry.
In general, cast iron has lower elongation, shrinkage, and impact toughness than cast steel, and its compressive strength and earthquake resistance are also better than cast steel; cast iron tends to be cheaper, while raw steel is more expensive and more expensive DEO comes at a higher material cost, energy and labor required to produce the final product. The main advantage of cast steel is design flexibility, allowing it to be used for complex shapes and hollow cross-section parts. They have their own advantages and disadvantages, so the choice should be made depending on the application and its physical properties.